OD Coating Systems
Choose the coating that best meets your customer needs, be it UV cure, thermal, or air dry coatings in a variety of colors. While galvanized tubulars and shapes provide considerable protection against corrosion, their performance and aesthetics may be further enhanced through application of a secondary coating or hybrid coating process. In addition to galvanized substrates, un-coated black mechanical tubes may utilize these secondary in-line processes to add utility, performance and value presenting many opportunities to non-galvanized tube and pipe producers. These secondary coating operations primarily act to shield the underlying substrates by forming a distinct protective barrier which insulates the surface from potentially harmful elements.
There are a number of coating technologies available for the many products which can be produced with the continuous galvanizing process. In general, each coating will also have process application technologies which is unique to each coating type. Below mentioned are the most prevalent coatings currently utilized over the outside diameter of galvanized tubulars and shapes.
Air dry coatings are formulations which require either little or no auxiliary heat source to cure the coating. Traditionally these are solvent rich lacquers which have relatively low solids contents and high solvent concentrations. These air-dry formulations may be clear or contain pigments to add colour to the surface of the product. This form of coating is considered to provide the least amount of corrosion protection and is generally utilized for short term storage protection. Electrical conduit is a suitable use for air dry coatings provided that inventories are only subjected to a moderately corrosive environment. Typically, air-dry coatings are applied by utilizing a flood and wiping apparatus. Dry film thickness is controlled by coating viscosity and wiping pressure with average films measuring approximately .0003". After application and wiping of the coating the solvents will evaporate or flash off and leave behind the thin film of solids as protection to the underlying zinc.
Heat cured coatings require a heat input generally provided by an induction or infrared heating unit to raise the tubing surface to a temperature where the coating becomes set or cures. These coatings are normally moderate in solids volumes and utilize a polyester resin or a water base, acrylic latex resin base. These coatings are most often clear but may in some cases utilize a pigment to both add colour as well as enhance corrosion performance. Heat cured coatings are considered to provide moderate to good corrosion protection for most tubular products and shapes (pipe, tube, square). Corrosion protection can be directly related and effected by the products pretreatment method, coating dry film thickness and continuity. Most heat dry coatings are applied with good results utilizing a flood and wiping system similar to that utilized in application of air-dry formulations. Dry film thickness is again controlled by coating viscosity with average depositions ranging from .0003" to as high as .0008" as dictated by the desired level of performance.
UV cured coatings are formulated with a photo reactive component which allows the coating to cure when an ultraviolet light source is introduced. UV cured coatings are virtually 100% solids by volume which means that no solvent component is present. This full solids content coupled with the high transfer efficiencies associated with current application equipment makes UV curables the only liquid coating technology which is essentially 100% efficient. An attribute only presently matched by powder systems. UV cured coatings can be applied by any of three means, flood and wiping, spray enclosure or vacuum applicator. Coatings again may be clear or pigment. Once applied to a wet film thickness of between .0005" and .001" dependent on desired protection, the product is passed through a series of lights which excite the photo reactive nature of the coating and an almost instantaneous cure is achieved UV cured coatings are primarily used when enhanced corrosion performance will substantially improve a products useful life and value.
REQUEST A CALL BACK
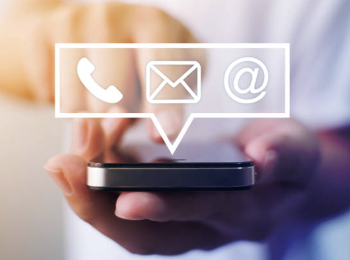